Coregas, one of the largest hydrogen, oxygen, nitrogen and argon producers in Australia, has been an integral part of the HESC project. The company is providing engineering consultancy, onsite support and equipment for the gasification plant at Loy Yang in the Latrobe Valley and the Australian first liquefaction and loading facility at Port of Hastings.
Paul Vandenbrink has a wealth of experience in the steel production and gas industries. In his new venture, working as a Site Manager in Hastings, he says, “It’s fantastic to see growing momentum for a hydrogen industry in Victoria and Australia. I’m excited to be part of this world-first project”.
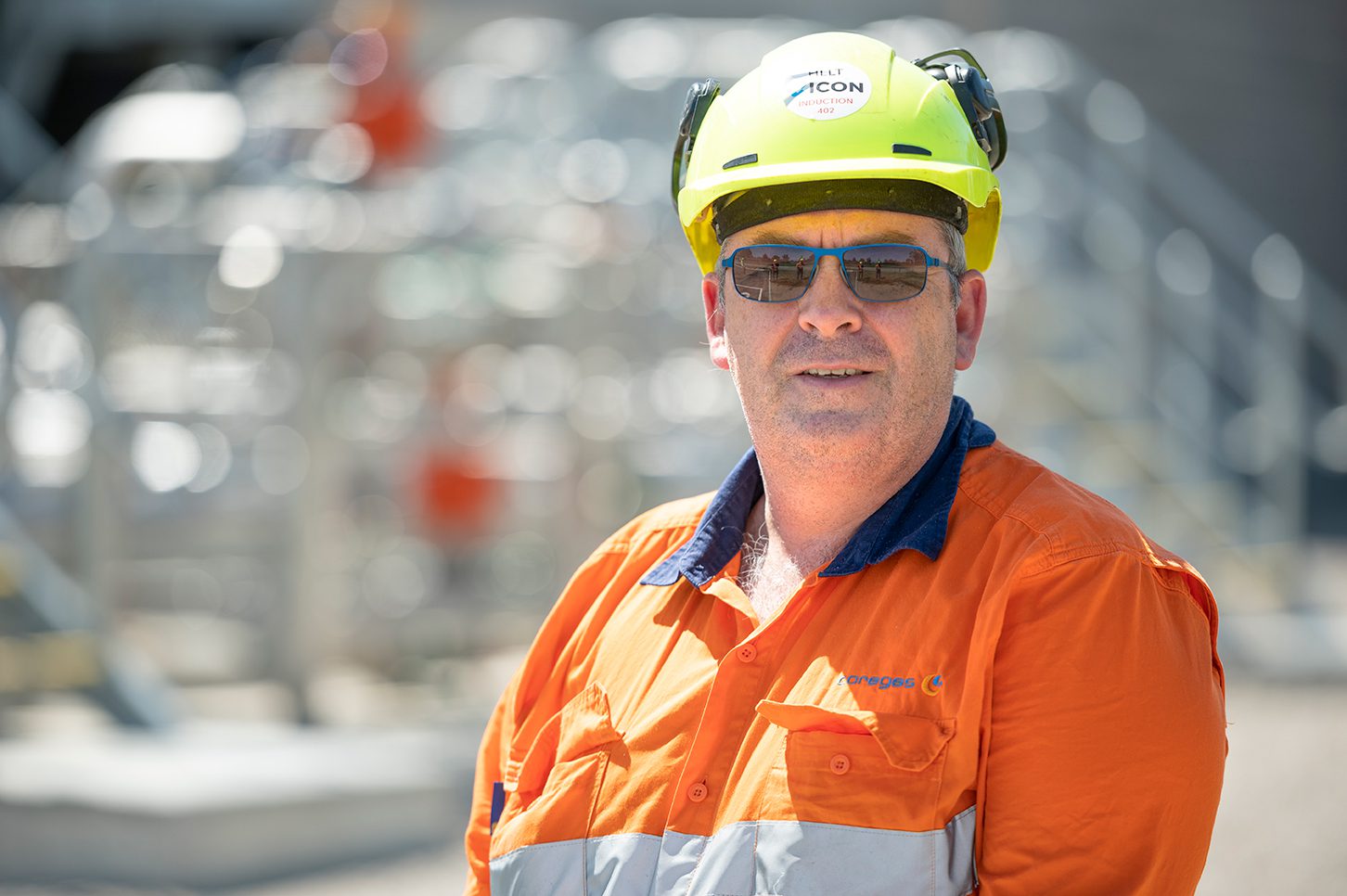
Mr Vandenbrink relocated from NSW six months ago and has settled in Mornington, which is close to Hastings.
“Coregas is proud to be involved in such an environmentally significant project like HESC and it’s exciting to step forward in the hydrogen energy industry as it is a demonstration of potential for a whole new export market and pathway to renewable energies” he said.
Coregas has been involved in the FEED (Front End Engineering Design) for the liquefaction plant in Hastings and has provided support for the detailed design of the plant. Further to this, Coregas is providing all the utility and specialised calibration gases to both facilities, the hydrogen compressor for the gasification plant and transportation services to move both liquefied and gaseous hydrogen.
A Coregas team of 12 is providing experienced engineering and maintenance support to run and maintain the liquefaction and loading facility in Hastings. The team belong to a company experienced at working with hydrogen – running the largest hydrogen merchant plant at Bluescope Steel’s Port Kembla steelworks.
Using this experience, Coregas’s expertise in the production and handling of hydrogen will be vital in the safe and efficient operation of the Hastings plant, as well as assisting with the loading of the world’s first liquid hydrogen carrier ship, the Suiso Frontier, when it arrives at the Port of Hastings this year. Coregas will also provide technical support at the Latrobe Valley site once operational.
When asked about the most interesting piece of equipment being used at the Hastings site, Paul spoke of the hydrogen liquefier, which has high-speed turbines, heat exchange and compression and expansion to create extremely cold temperatures of -253 degrees Celsius.
Working on the project during COVID-19 hasn’t been without its challenges. COVID restrictions meant a 25% restriction of the number of people on-site, work and travel permits needing approval and deep cleans being required at the sites. Furthermore, the lack of toilet paper, hand sanitiser and masks presented more of a challenge. Nonetheless, Coregas implemented a COVIDSafe plan and successfully maintained operations during the tough period.
When asked about working with HESC project partner Kawasaki Heavy Industries (KHI), Mr Vandenbrink said, “It has been an honour to work with the reputable team at KHI. We have been able to learn a lot about each other’s culture and together we have collaborated to deliver this fantastic initiative”.
Note on the hydrogen liquefier: The hydrogen liquefier works by pressurised hydrogen gas being fed into a vacuum-insulated cold box and getting pre-cooled with liquid nitrogen. Pre-cooled hydrogen gas is heat-exchanged with liquefied helium, which is produced from helium refrigeration cycle, then it is turned into liquid and transferred to an LH2 container.