Mass quantities of liquefied hydrogen have not been shipped across open waters before, but the newly built SUISO FRONTIER overcomes the challenges of transportation. The ship will play a key role in realising the HESC Project’s world-first demonstration of a hydrogen supply chain between Australia and Japan.
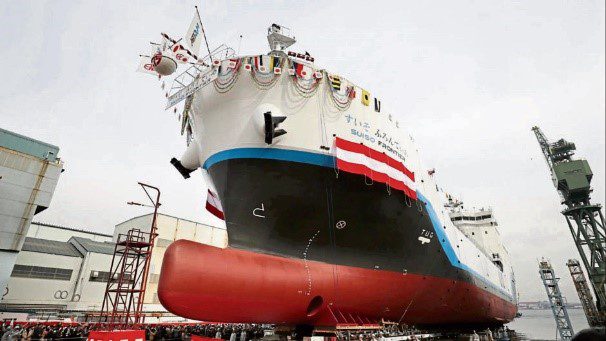
When hydrogen gas is liquefied, it becomes denser to the point of 1/800 of its original gas-state volume.
This highlight the benefits and challenges of transporting liquid hydrogen.
Over longer distances it is usually more cost-effective to transport hydrogen in liquid form, since a liquid hydrogen tank can hold substantially more hydrogen than a pressurised gas tank. However, preventing heat from turning the liquid hydrogen back into a gas – known as ‘boil off’ – presents unique challenges.
During the HESC Project, the 116-metre-long SUISO FRONTIER will make one trip between Australia and Japan every few months. On board will be a crew of no more than 25 people.
To prevent boil off during its journey, HESC project partner and shipbuilder Kawasaki Heavy Industries, Ltd. (KHI), developed specialised insulation technology.
The 1,250m3 storage tank is a world-leading and game-changing technological development likely to boost the global hydrogen economy.
It features a cryogenic storage element, a double-shell structure with vacuum insulation and is supported by high strength glass-fibre-reinforced plastic. It contains the liquefied hydrogen and keeps it at -253 degrees Celsius.
Much of the ship’s features are a progression of technology originally developed in 1981, when KHI became the first Asian company to manufacture a liquefied natural gas (LNG) carrier.
Thirty years later, SUISO FRONTIER will play a pivotal role in realising the potential for the HESC Project to kick-start a new, global clean energy export industry with huge local economic benefits for both Australia and Japan.